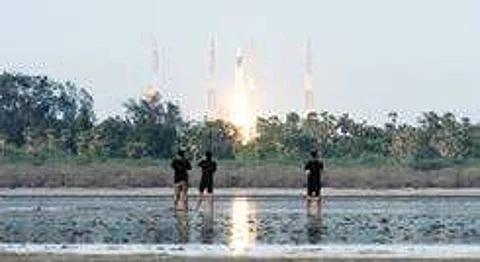
CHENNAI: There is no time to relax for scientists at the Indian Space Research Organisation (ISRO), who have just launched India’s heaviest rocket, GSLV MkIII, fitted with home grown high-thrust cryogenic stage.
Buoyed by the success, the space agency has now set its eyes on a 10-tonne payload launcher for which semi-cryogenic engine is being readied. This engine is 10 times more powerful than CE20 in terms of the thrust it delivers.
ISRO Propulsion Complex (IPRC) at Mahendragiri in Tirunelveli district, which developed two core stages, L110 and C25 for GSLV MkIII, and Liquid Propulsion Systems Centre (LPSC) at Thiruvanathapuram are playing the key role.
LPSC is responsible for design and IPRC will be doing assembly, integration and testing. Civil works for building infrastructure to carry out series of tests have reached final phase in at IPRC and the fabrication of six critical subsystems for development of semi-cryogenic engine (SCE200) is being done by different industries.
PV Venkitakrishnan, Director, IPRC, told Express that this next generation engine uses a combination of liquid Oxygen and Isrosene (purified Kerosene) as propellants which are cost-effective and eco-friendly.
“Already, a sample of Isrosene has been prepared and qualified. SCE200 will replace L110 stage of GSLV MkIII. This will immediately enhance the GTO payload capability from four to six tonnes, and can be expanded up to 10 tonnes. We plan to have an (semi-cryogenic) engine and stage capable of flight by 2020 and try it on GSLV-MkIII,” he said.
The full duration of SCE200 is 310 seconds, just half C25. But, it delivers 200 tonnes of thrust and uses about 210 tonnes of propellant. This is a real monster, which throws up engineering challenge for scientists and the industry.
Semi-cryogenic engines are part of ISRO’s bigger game plan to develop modular vehicle, also called Unifield Launch Vehicle (ULV), as it is highly expensive to operate different launch vehicle for different payloads and takes around 10-15 years to develop a launch vehicle. So, a better option is to have a single launch vehicle and tweak the stages, propellant loading etc to launch different classes of satellites.
Genesis
In 2008, ISRO initiated a programme to develop semi cryogenic engine technology to allow low cost access to space
Using this engine, a semi cryogenic stage will be developed that will constitute the core stage of ISRO’s future launch vehicles - ULV and reusable launch vehicles or RLV
Semi cryogenic engine has efficiency and cost advantages over engines that use solid and hypergolic liquid propellants. The specific impulse of semi cryogenic engine is higher than others, which means that it can lift a higher payload for the same propellant mass
Its propellants are safer to handle and store. The engine uses a combination of liquid Oxygen and Isrosene (purified Kerosene) as propellants which are cost-effective and eco-friendly